Wright Coating Technologies offers four (4) unique Powder Coating lines to match your job requirements for your industrial or commercial application. All four lines incorporate automated and manual processing. There is a wide array of colors available for both functional and aesthetic applications.
Our commercial and industrial powder coating services are extensive, impressive, and one of our most requested specialty coating applications. We are an ISO 9001:2015 registered coatings applicator that places a strong emphasis on meeting and exceeding expectations to ensure quality powder coatings.
Applications are also available for applying Epoxies, Polyesters, Urethanes, Vinyl, and Nylons.
Wright has developed expertise in a wide range of industries, including applying powder coatings for the alternative energy, appliance, automotive, consumer goods, metal fabricator, fitness equipment, outdoor grills, and office furniture industries. We also provide very cost-effective coating solutions to resolve BSR and NVH issues in the automotive industry. We provide these and many more custom powder coating services as needed.
Learn More
Is Powder Coating Better Than Painting?
Powder coatings provide better performance than traditional wet painting as it is more rugged and resistant to corrosion, chemicals, and weathering. Powder-coated surfaces also resist chipping, scratching, and other wear much more effectively than wet paint. Typically wet paint should be used in applications where the material being finished cannot withstand the heat necessary for powder coating. In nearly every other scenario, powder coating is more superior. Powder coatings are less expensive in comparison to paint and can cover more area than most finishers, which means lower material costs than wet painting processes.
Traditional wet paint is also extremely flammable and contains carcinogens and volatile organic compounds (VOCs). Not surprisingly, these chemicals are hazardous to plant employees if proper precautions are not met. Powder coatings do not contain VOCs and are without solvents, meaning they pose much less of a chemical risk to workers. Beyond being a risk to workers, VOCs and solvents also create a pollution concern. Powder coating is a much cleaner process, as well. Overspray can be gathered and reused, and unused powder can be retrieved and put back in a hopper for recirculation, eliminating a lot of waste.
Powder Coating Advantages
There are several advantages to powder coating over conventional liquid coatings:
- Powder coatings emit zero or near zero volatile organic compounds (VOC)
- Powder coatings can produce much thicker coatings than conventional liquid coatings without running or sagging
- Powder coating overspray can be recycled making it possible to achieve nearly 100% use
- Powder coating production lines produce less hazardous waste than conventional liquid coatings
- Powder-coated items generally have fewer appearance differences between horizontally and vertically coated surfaces than liquid coated items
- A wide range of specialty effects are easily accomplished which would be impossible with other coating processes
- Able to handle small parts up to 26” x 12” x 52”
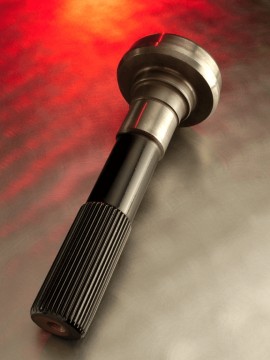
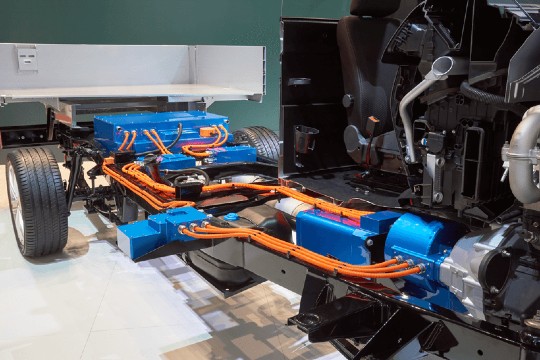